Principles, Characteristics, Applications, and Process of Injection Molding
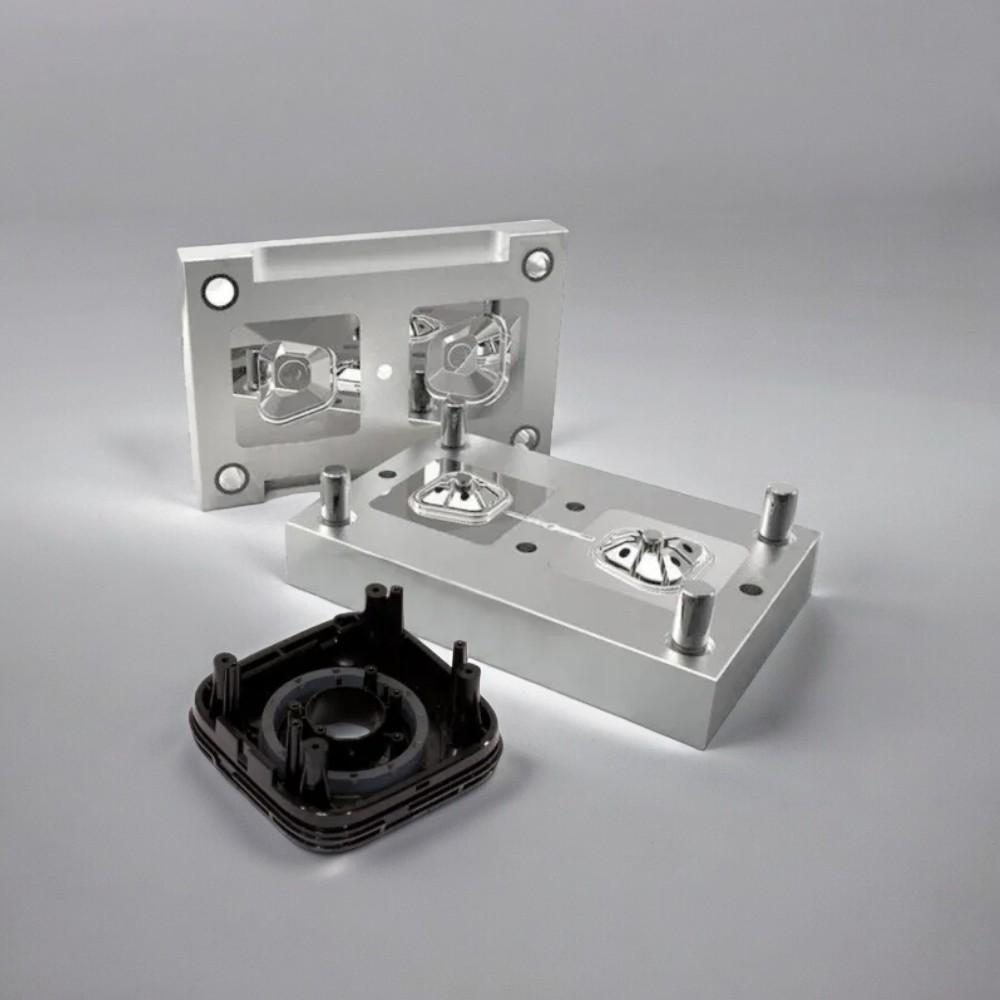
Injection molding is a widely utilized plastic processing technique essential for the production of diverse plastic products. This article offers an in-depth exploration of injection molding principles, characteristics, advantages, disadvantages, applications, and the detailed process involved, including insights into the Ultirapid Injection Molding system.
Injection molding is a fundamental method in plastic manufacturing, renowned for its efficiency and versatility. Through this article, I aim to provide a comprehensive overview of injection molding, encompassing its underlying principles, distinctive features, practical applications, and the intricate processes involved.
Principles of Injection Molding
Injection molding functions by introducing granular or powdered plastic into a hopper connected to an injection machine. Inside the machine, the plastic is heated to a molten state. This molten plastic is then injected into a closed mold cavity under controlled pressure. After cooling, the plastic solidifies into the desired component shape, ensuring precision and consistency.
Characteristics of Injection Molding
Injection molding is known for its rapid production cycles and high productivity. It supports the creation of complex shapes with tight tolerances and allows for the integration of various inserts. The process is highly conducive to automation, enabling automated operations such as injection, mold release, and gate removal, which enhances overall efficiency.
Advantages of Injection Molding
Short Cycle Time and High Efficiency: The process is optimized for swift production, minimizing overall manufacturing time. Automation Friendly: Injection, demolding, and gate removal can be fully automated, streamlining the process. Complex and Precise Parts: Capable of producing intricate shapes with high dimensional accuracy and accommodating metal or non-metal inserts. Consistent Product Quality: Provides stable quality and reproducibility across production runs. Broad Application Range: Suitable for a wide variety of thermoplastics and some thermosetting plastics. Disadvantages of Injection Molding
High Equipment Cost: The initial investment in injection molding machines and molds can be substantial. Complex Mold Design: The design and fabrication of molds are often intricate and costly. High Production Costs: The complexity of equipment and molds can lead to elevated production costs. Longer Production Setup: Although cycle times are short, setup times for molds can be lengthy. Not Ideal for Small Batch Production: Less cost-effective for low-volume manufacturing runs. Applications of Injection Molding
Injection molding is applicable to nearly all thermoplastics and is also effective for molding thermosetting plastics, enhancing its versatility. This method is crucial across industries such as automotive, consumer goods, and medical devices, offering a wide range of applications.
Injection Molding Process
The injection molding process includes several stages:
Pre-Processing Preparation: Involves raw material inspection, determining processing properties, preheating and drying plastics, barrel cleaning, preheating inserts, and selecting mold release agents. Injection Phase: Consists of material feeding, melting, mold filling, pressure holding, cooling post-gate solidification, and demolding. Post-Processing: Includes annealing and moisture conditioning to achieve optimal properties of the molded parts. Injection Molding Process Parameters
Key parameters include:
Temperature: Includes barrel temperature, nozzle temperature, and mold temperature. Pressure: Covers both plasticizing pressure and injection pressure. Time: Refers to the total time required to complete a molding cycle, known as the injection molding cycle time. Development of Plastic Molding Process Guidelines
Formulating effective plastic molding process guidelines involves selecting the appropriate molding method based on product requirements and plastic characteristics. This includes determining process conditions, designing molds, selecting equipment, and developing process documentation to ensure efficient molding and high-quality component production.
Ultirapid Injection Molding
Ultirapid Injection Molding represents a significant advancement in this field, offering state-of-the-art technology that enhances both efficiency and precision. The Ultirapid system is designed to optimize the molding process with advanced automation capabilities and superior control over temperature and pressure. Its implementation can significantly reduce cycle times and production costs while improving the overall quality of molded parts.
Conclusion
Injection molding is an advanced and highly efficient technique for manufacturing a diverse range of plastic products. By understanding its principles, benefits, and intricacies, including innovations like Ultirapid Injection Molding, one can optimize application and process management in various industrial contexts.
- Art
- Causes
- Crafts
- Dance
- Drinks
- Film
- Fitness
- Food
- الألعاب
- Gardening
- Health
- الرئيسية
- Literature
- Music
- Networking
- أخرى
- Party
- Religion
- Shopping
- Sports
- Theater
- Wellness
- Travels