Understanding Key Metal Additive Manufacturing Technologies: A Guide to Process Selection
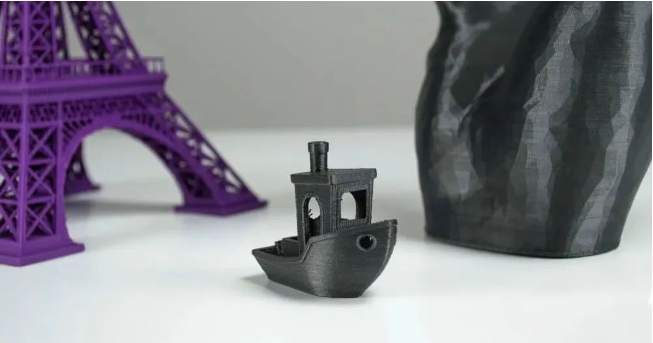
In the past decade, metal additive manufacturing (AM) technologies have proliferated, with several achieving significant industrial maturity. Prominent among these are Powder Bed Fusion (PBF), Direct Energy Deposition (DED), and Binder Jetting (BJ). Each of these techniques produces parts with distinct mechanical properties, microstructures, and physical characteristics due to their unique process methodologies. Understanding these characteristics is crucial for end-users when selecting a suitable AM process that meets specific application requirements. This article explores the differences and similarities between these three major technologies and their impact on part performance.
Powder Bed Fusion (PBF)
-
Surface Roughness: Typically ranges from 5 to 15 µm, influenced by factors such as powder particle size, layer thickness, and scanning strategies.
-
Thin-Wall Structures: Capable of high resolution, PBF is suitable for producing thin-wall structures with thicknesses between 100 and 200 µm.
-
Dimensional Accuracy: Generally within ±0.05 to ±0.2 mm, depending on process parameters and equipment calibration.
-
Part Density: Typically achieves over 99%, approaching the density of forged parts.
-
Build Rate: Laser PBF speeds range from 10 to 30 cm³/h, which can be increased with multiple lasers, high power, large layer thicknesses, and large spot sizes; Electron Beam PBF offers slightly higher speeds of 50 to 100 cm³/h.
-
Mechanical Properties: High strength, hardness, and wear resistance, usually outperforming parts produced by traditional manufacturing methods.
-
Advantages: Capable of producing complex geometries with excellent mechanical properties and high dimensional accuracy, ideal for precision parts.
-
Challenges: Often requires post-processing, such as machining or polishing, to achieve optimal surface finish. Thermal stress and warping may affect accuracy, necessitating careful support structure design and process parameter optimization. Production rates are relatively low, making it suitable for small-batch, high-precision parts, with residual stresses often requiring heat treatment and additional post-processing.
Direct Energy Deposition (DED)
-
Surface Roughness: Generally higher than PBF, with Ra ranging from 10 to 50 µm, affected by feed rate, energy input, and deposition strategy.
-
Thin-Wall Structures: Typically challenging to produce walls thinner than 500 µm.
-
Dimensional Accuracy: Generally within ±0.2 to ±1 mm, with relatively lower precision.
-
Part Density: Usually between 95% and 99%, influenced by process parameters and materials.
-
Build Rate: Higher, typically between 200 and 500 cm³/h.
-
Cooling Rate: Relatively low, usually between 10³ and 10⁴ K/s.
-
Mechanical Properties: Good strength and hardness, depending on process parameters and material type, generally suitable for large structural components.
-
Advantages: Suitable for manufacturing and repairing large parts with high material utilization.
-
Challenges: Higher surface roughness often requires extensive post-processing. Due to high thermal input, thin-walled sections may suffer from accuracy and surface finish issues, with potential for thermal distortion.
Binder Jetting (BJ)
-
Surface Roughness: Typically ranges from 5 to 20 µm.
-
Thin-Wall Structures: Capable of producing thin-wall structures with thicknesses between 300 and 500 µm.
-
Dimensional Accuracy: Generally within ±0.1 to ±0.5 mm, affected by the sintering process and powder characteristics.
-
Part Density: Typically between 85% and 95%, with density further increased after sintering.
-
Build Rate: Fast, usually between 1000 and 2000 cm³/h (for green parts only).
-
Cooling Rate: Dependent on the sintering process, generally low, around 10² to 10³ K/s.
-
Mechanical Properties: Can achieve high strength after sintering, though typically lower than PBF and DED, suitable for medium-strength applications.
-
Advantages: No thermal stress, capable of producing highly complex parts at a lower cost.
-
Challenges: Sintering may cause shrinkage and surface texture changes, affecting dimensional accuracy of thin-walled structures. Density is usually lower compared to parts made using melting-based processes. Despite the faster printing process, the sintering phase is time-consuming, affecting overall production time and part quality. Precise control during sintering is crucial for uniform cooling and dense structures.
Summary
Understanding the characteristics and adaptability of different metal additive manufacturing technologies is essential for selecting the right process. By comparing PBF, DED, and BJ, users can better assess their production needs and make informed choices to achieve optimal part performance and production efficiency.
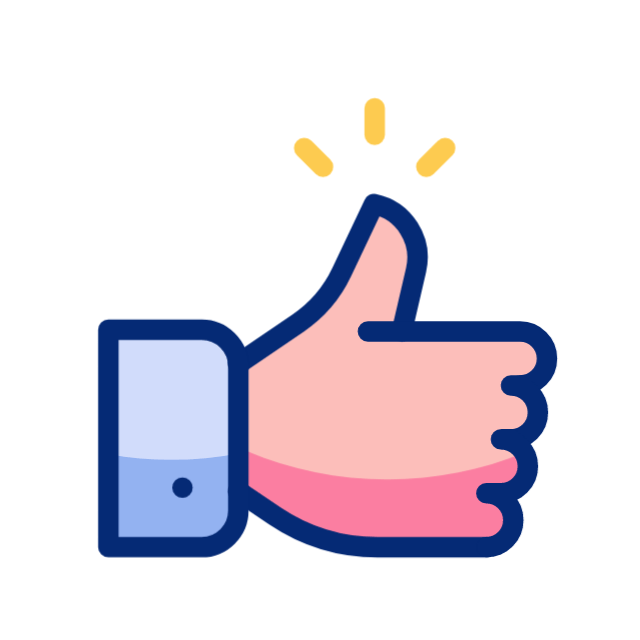
- Art
- Causes
- Crafts
- Dance
- Drinks
- Film
- Fitness
- Food
- Oyunlar
- Gardening
- Health
- Home
- Literature
- Music
- Networking
- Other
- Party
- Religion
- Shopping
- Sports
- Theater
- Wellness
- Travels